The Latest Innovations in Chemical Defoamer Technology for Enhanced Efficiency
The Latest Innovations in Chemical Defoamer Technology for Enhanced Efficiency
Blog Article
Recognizing How a Chemical Defoamer Works to Improve Industrial Processes
Chemical defoamers play a pivotal duty in maximizing commercial processes by effectively mitigating foam-related obstacles. What continues to be to be checked out is exactly how these defoamers can be tailored to fulfill certain operational demands.
What Is a Chemical Defoamer?
A chemical defoamer is a material especially developed to decrease or eliminate the development of foam in different industrial procedures. Lathering can disrupt manufacturing effectiveness, affecting the top quality and efficiency of products in fields such as food and drink, pharmaceuticals, and wastewater therapy. Defoamers are important in these applications, as excessive foam can bring about operational challenges, such as overflow, lowered mixing performance, and impeded heat transfer.
The choice of an ideal defoamer is necessary, as various formulas might be customized for particular procedures or types of foam. Elements such as compatibility with various other ingredients, temperature security, and the desired application play a significant function in the performance of a defoamer.
Mechanisms of Defoaming Action
The devices of defoaming activity entail intricate interactions between the defoamer and the foam structure. When a defoamer is introduced to a foaming system, it migrates rapidly to the surface of the foam bubbles, displacing the supporting agents that contribute to foam stability.
As smaller bubbles merge into larger ones, the overall stability of the foam decreases. Additionally, certain defoamers may contain hydrophobic elements that boost their ability to destabilize the foam by creating a barrier that hinders bubble development. This twin activity-- surface area tension reduction and destabilization-- allows for a more efficient breakdown of foam.
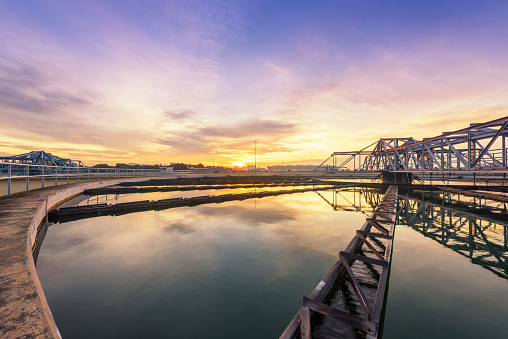
In addition, the thickness and spreading qualities of the defoamer play essential roles in its performance. A well-formulated defoamer will certainly guarantee rapid migration and optimum performance, reducing foam formation throughout industrial processes. By recognizing these systems, industries can much better choose and apply chemical defoamers to boost functional efficiency and item high quality.
Sorts Of Chemical Defoamers
Chemical defoamers can be categorized right into a number of types, each customized to particular applications and foam challenges. The main classifications consist of silicone-based, non-silicone-based, and powder defoamers.
Silicone-based defoamers are very effective due to their ability to spread out rapidly across fluid surfaces. Non-silicone-based defoamers, on the various other hand, often depend on natural compounds like fatty acids or esters.
Powder defoamers are composed of solid bits that can be contributed to dry processes or formulations. They are commonly utilized in procedures where fluid defoamers might not work, offering an one-of-a-kind service for details applications, such as in the production of specific kinds of plastics or powders.
Furthermore, each kind of defoamer can be customized with different ingredients to boost effectiveness, such as surfactants or emulsifiers, permitting for versatility in dealing with various frothing scenarios across several sectors.
Applications in Industrial Processes
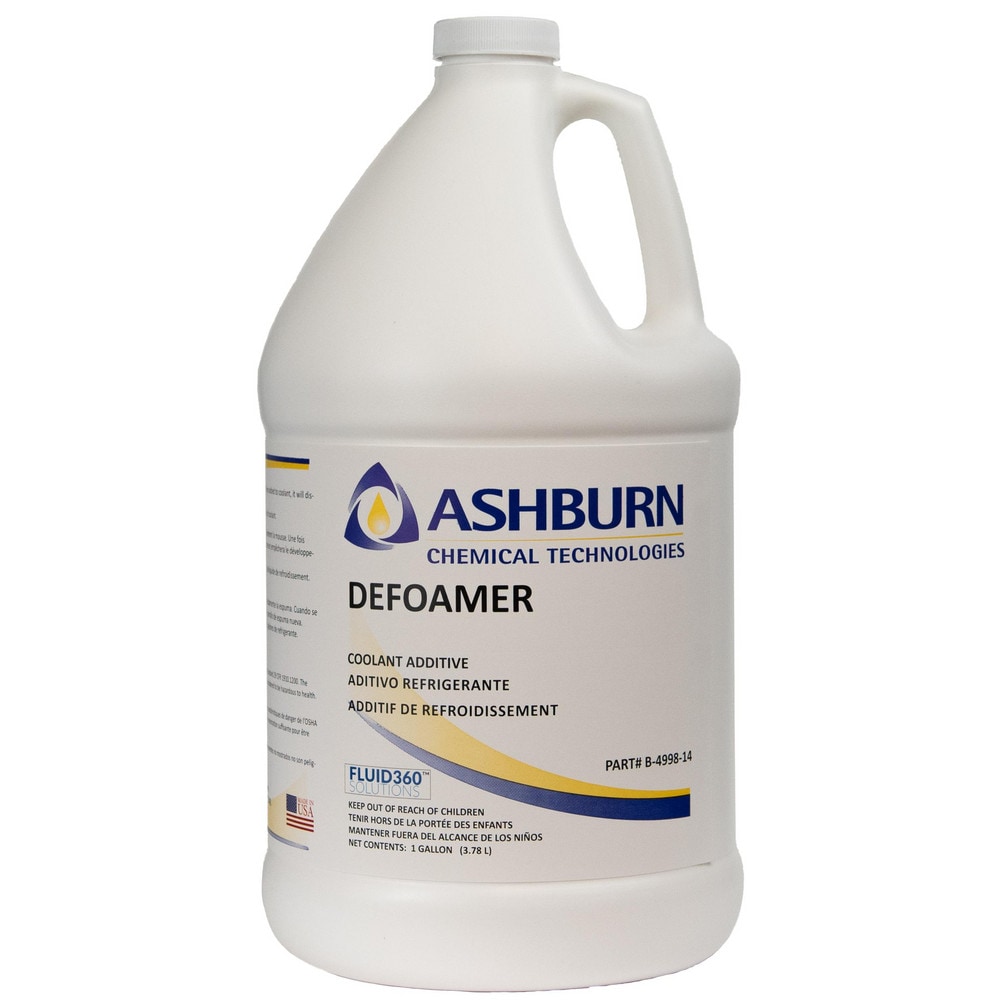
In the food and drink industry, defoamers are critical throughout the production of juices, beers, and milk products, where too much foam can hinder blending and filtering procedures. By minimizing foam formation, defoamers assist maintain constant product high quality and optimize handling times.
In pharmaceuticals, the existence of foam during the mixing and solution of medicines can influence dosage precision and product security. the original source Defoamers ensure smooth operations, therefore assisting in the production of premium drugs.
Wastewater treatment centers also depend on defoamers to regulate foaming in oygenation tanks, which can otherwise lower treatment effectiveness and make complex sludge handling. By efficiently handling foam, these chemicals boost the overall efficiency of therapy processes and contribute to governing conformity.

Advantages of Utilizing Defoamers
While foam can provide significant challenges throughout numerous markets, the use of defoamers provides numerous advantages that boost operational efficiency and product honesty. Defoamers successfully minimize or get rid of foam development, resulting in smoother production procedures and enhanced product top quality. This decrease in foam reduces disruptions throughout manufacturing, permitting continual procedure and increased throughput.
In addition, the application of defoamers can cause cost financial savings by reducing the need for excess raw products and energy consumption linked with foam administration. By optimizing the my review here manufacturing process, suppliers can accomplish greater yields and reduced waste, eventually improving earnings.
Additionally, defoamers add to much better tools performance. Foam build-up can result in obstructing, overflow, and devices wear, causing expensive downtime and upkeep. By avoiding these concerns, defoamers prolong the life-span of machinery and lower operational expenses.
Conclusion
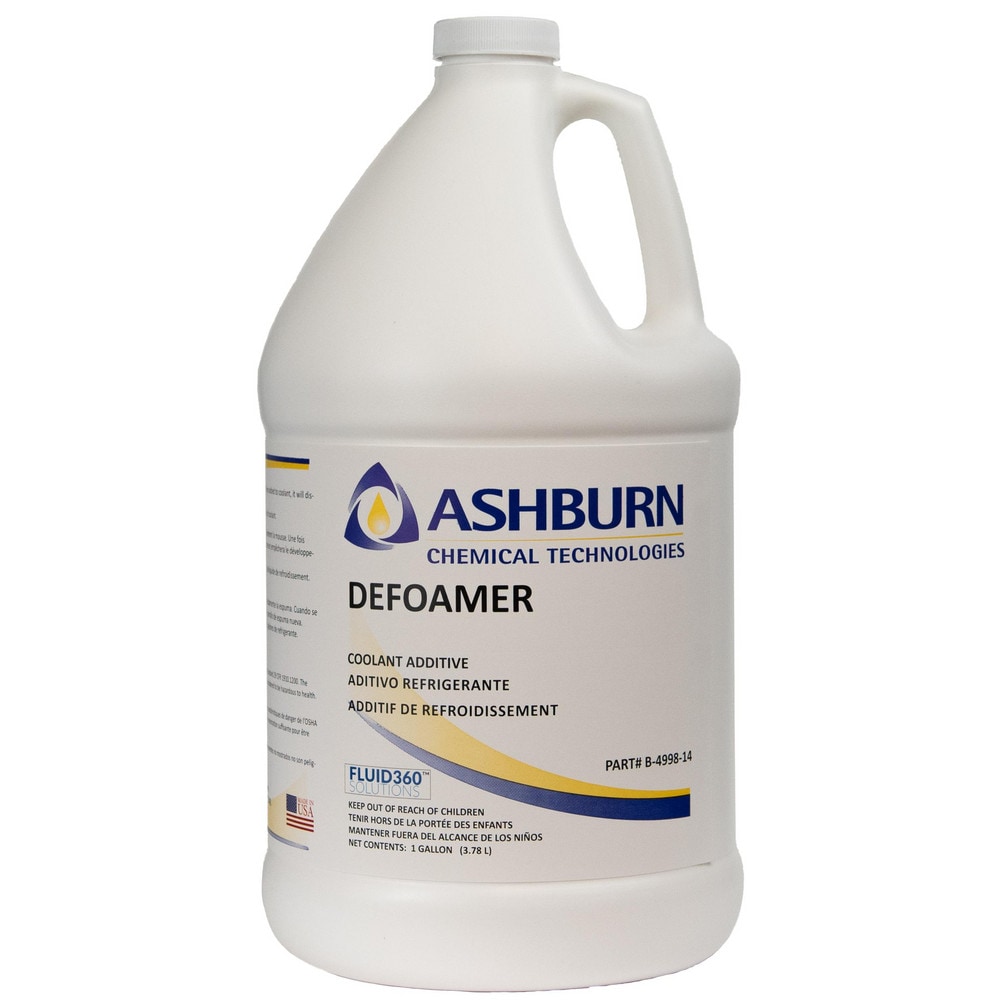
A chemical defoamer is a compound specifically created to decrease or eliminate the development of foam in various commercial processes. When a defoamer is presented to a lathering system, it migrates quickly to the surface of the foam bubbles, displacing the maintaining agents that add to foam stability. A well-formulated defoamer will certainly guarantee rapid movement and optimal efficiency, minimizing foam development during commercial processes. Defoamers successfully eliminate or minimize foam formation, leading to smoother manufacturing procedures and enhanced item quality.In verdict, chemical defoamers play an important duty in enhancing commercial procedures by efficiently lowering foam formation.
Report this page